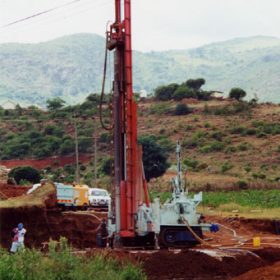
Application | Socket Piles for Bridge Support |
---|---|
Location | Northern Province, South Africa |
Hammer | Challenger 125 Hammer |
Bit | Super Jaws® T410 Overburden Bit |
Hole Size | 18 inch (457 mm) |
Depth or Length | 13 - 46 feet (4 - 14 m) |
Formation | Overburden, Silt, Gravel, Hard Boulders, Sandstone |
Rig Type | Atlas Copco Rotamec (Modified) |
Description
In the first few months of the year 2000, some of the heaviest rains ever recorded fell in the mountainous area of the Northern Province in South Africa. Some of the hardest hit areas were along the route to Mozambique where flooding waters destroyed ten (10) major bridges and numerous minor road crossings. Although many of the minor crossings have since been repaired with preformed culverts, a massive bridge rebuilding project has been undertaken to restore the transportation routes.
The reconstruction of the bridges was no small undertaking as some 300 drilled piles were required for installation of new spans over the waterway. The contractor had the support and service of Numa’s local distributor, Deed Drilling Supplies (DDS).
The project required 18 inch (457 mm) piles to be drilled down through an extremely unconsolidated formation of overburden, silt, gravel, hard boulders and finally socketing into sandstone bedrock. Also needing consideration was the close proximity to the water formation. The top of the pile was required to be approximately 3-1/4 feet (1 m) above water level and 10 – 26 feet (3-8 m) from the river edge.
The contractor had previous experience drilling in formations containing vast amounts of boulders but unfortunately encountered many problems with the eccentric drilling systems they had employed. Most of these problems relate to the overall design of eccentric systems that allow for only part of the bit to be in contact with the formation at any given time. If boulders are encountered, the bit system must rotate all the way back around to strike the boulder again. In the mean time, the casing is advancing and striking the boulder which can cause excessive binding and torque build up. Eventually this results in failure.
The contractor investigated many different styles of drilling for this project, but after careful consideration they chose Numa Challenger 125 down hole hammers and Super Jaws® Under Reaming Bits due to their ease of operation. The Super Jaws® Bit, manufactured by Numa under rights from the Tone Corporation, is a special under reaming wing bit design made for simultaneously setting casing while drilling. It is engineered to have wings extend out further than the casing while in the drill position to allow casing to be pulled down the hole while drilling. The under reaming concept allows the full face of the bit to be in constant contact with the rock formation to easily break up boulders and any other rock formations encountered. This lowers the torque and reduces the possible damage to the rotation head motor as well as lowering the possibility of a shank failure. The under reaming bit also does not require the use of costly replacement ring bits or casing shoes that remain down the hole when drilling is complete. Once drilling is complete, the wings retract back inside the casing and the entire bit is brought to the surface while the casing is left securely down the hole.
In order to complete the down hole hammer drilling, an Atlas Copco Rotamec crawler drill was modified for this project. It had approximately 18,000 Nm of torque and 35 tons of pull back with a selection of rotary speeds up to 40 rpm. Air requirements were satisfied with Atlas Copco XRHS 385 825 x 290 and IR 900 x 170 compressors that were used to produce 170 psi (12 bar). Coupled together, the two compressors were able to account for the correction factor required for air temperature of 85° F and an altitude of 6750 feet (2059 m).
Two (2) test holes 29-1/2 feet (9 m) deep were drilled near Pretoria prior to departure to the project site in order to test the rig and make any changes. In a formation of dense shale and diorite, the Numa hammer and Super Jaws® bit drilled a 29-1/2 foot (9 m) casing in approx 42 minutes with a working pressure of 130 psi (9 bar). With the overwhelmingly positive test results under their belt, the contractor moved the drilling system on-site to begin operation.
Out at the drill site, the required depth for the 18″ (457 mm) diameter piles varied from 13 – 46 feet (4 -14 m) with the most common depth around 29-1/2 feet (9 m). Foam was used to properly clean the casing due to the large annulus resulting in large hammer drilling. By injecting approx 6 GPM of Baroid Aerofoam mixed with approximately 2% of volume of river water, the system produced a mix of cuttings up to 1″ x 2-1/4″ (25.4 – 57.2 mm). Lubrication was via venturi and used Petromark Rockdrill 320 which is a local equivalent of Shell Torcula 320. The overall flow rate was approximately 2-1/2 gallons (10 litres) per hour. On the very first hole, the Numa hammer and bit drilled a 29-1/2 foot (9 m) hole within 30 minutes in a formation consisting of 5 feet (1.5 m) overburden / backfill, 9 feet (2.8 m) silt, 10 feet (3 m) stones / shingle / boulders and 7 feet (2 m) of dense sandstone bedrock.
The Numa hammer and Super Jaws® bit successfully completed the job drilling without hesitation and aggressively installing casing 7 feet (2 m) into bedrock. Once holes were completely drilled, the removal of the casing was easily completed with the rig or the site crane. Throughout the drilling process, Deed was on site to provide technical support and service. Contractors on the project noted it was very impressive to see casing going down so quickly in such difficult conditions.
Get to the bottom of it with Numa.