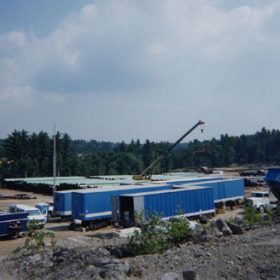
Application | Pipeline Expansion |
---|---|
Location | New Hampshire, Eastern USA |
Hammer | Numa 180 Hammer |
Bit | Impact Ring Bit System® |
Hole Size | 26 inches (660 mm) |
Depth or Length | 40 - 160 feet (23 - 49 m) |
Formation | Overburden, Boulders, Granite |
Rig Type | American Auger 48 with Barbco Modifications |
Description
Tennessee Gas and El Paso Energy have set out to dramatically expand their pipelines in order to better meet rising energy demands in the United States. This growth policy has resulted in several major gas pipeline expansions in the northeastern United States. Once completed, this pipeline will stretch a total of 21 miles (34 km).
The existing pipeline being expanded called for 8-inch (203 mm) diameter pipe to be upsized to 20-inch (508 mm) diameter in order to facilitate an increased flow of gas. The most demanding part of this project called for drilling seven (7) bores in formations consisting of overburden, boulders and granite. Each bore required drilling a 26-inch (660 mm) diameter hole under highways and roads in various lengths between 40 to 160 feet (12 – 49 m) long. To further complicate matters, much of the installation points were in close proximity to existing water and gas utility lines so impact to surrounding areas had to be kept to a minimum. The two energy companies contracted Gregory and Cook based out of Houston, TX in order to complete the installation.
In the past, Gregory and Cook had extremely bad experiences with installing underground pipelines in ground formations consisting of rocks and boulders. Typically they employed the use of augers that drilled very slowly when encountering any rock conditions and caused long delays in the pipeline installation process. Gregory and Cook turned to Western Supplies of Wichita Falls, Texas for some assistance. Long considered experts in the horizontal drilling industry, Western Supplies gladly accepted the challenge.
As they typically do on most drilling projects, Western Supplies came to the job site with tractor trailers full of every conceivable supply that may be required to successfully complete the project. Experienced staff was also placed at the job to thoroughly train and support the energy companies throughout the life of the project on the latest techniques for efficiently drilling and installing pipelines in difficult conditions. Part of the equipment that Western Supplies brought with them was a Numa 180 down hole hammer and a 26″ (660 mm) Impact Ring Bit System®, both of which played a critical role in this project’s success.
The Impact Ring Bit System® consists of a unique two-piece design incorporating a center and ring bit combination. The center bit is attached directly to the DTH hammer that is used to power the drilling while the ring bit is welded to the casing being installed. The hammer and center bit are inserted through the casing and the two bits work in unison to install the casing while drilling. Upon completion of the hole, the center bit and drill string can be pulled back out of the hole leaving the casing installed. The ring bit is also fully recoverable in horizontal applications that utilize pit-to-pit drilling techniques. This provides the added benefit of lower equipment costs because the product can be used again and again on multiple projects.
To install the pipeline, a drilling system consisting of a Numa 180 down hole hammer with a 26″ (660 mm) Impact Ring Bit System® was utilized. The hammer and bit were powered by an American Auger 48 with Barbco modification boring rig with two Sullair 1300 cfm / 150 psi (614 l/sec / 10.2 bar) air compressors that were able to supply 2600 CFM / 125 PSI (1227 l/sec / 8.5 bar). The drilling system also included the use of hollow stem augers behind the hammer to facilitate cleaning the hole while drilling. Hollow augers are used instead of solid ones to allow the air to flow from the compressors to operate the down hole hammer.
When the project encountered a highway, Gregory and Cook had to decide if they wanted to dig up the highway to install casing or try to drill underneath it. The decision was an easy one as drilling underneath would save considerable amounts of time and money because there would be no need to dig up the road, congest traffic, repave surfaces and increase insurance liability for workers. Western Supplies was able to train their customer how to set-up their boring rig on one side of the highway to drill straight through without disturbing anything on the surface. The process was very simple as the hammer and ring bit system was laid horizontally in the rig. The rig powered the drilling system to tunnel through rock while simultaneously pulling 24-inch (610 mm) OD steel casing under the highway. After the hammer and bit exited the rock formation on the other side of the highway, the ring bit was removed from the end of the casing and the hammer and center bit were pulled back through the installed pipe. A 20-inch (508 mm) concrete-coated pipe to be used to transport the gas was then inserted inside the casing. This allowed Gregory and Cook to completely remove the 24-inch (610 mm) pipe. With the pipeline successfully installed, the hammer, center and ring bit were then ready to be used on the next rock tunneling location.
The conditions on this pipeline project were difficult but not as demanding and time consuming as they could have been if Western Supplies had not introduced their customer to some exciting new technology in the way of Numa hammers and the Impact Ring Bit System®. Over the course of the project, the average penetration rate in overburden condition was an outstanding 15 feet (4.5 m) per hour. This leap in performance over conventional methods so impressed Gregory and Cook that instead of renting the Numa Impact Ring Bit System®, they decided to buy it because they saw the tremendous cost savings it would return to them on many projects down the road.
Get to the bottom of it with Numa.