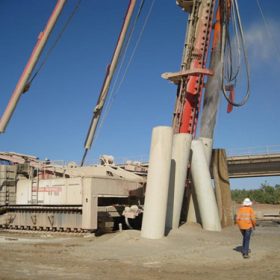
Application | Advancing tubular steel piles to bedrock & drilling rock sockets below the pile toe |
---|---|
Location | Pilbara Region, Western Australia |
Hammer | Champion 330 |
Bit | Super Jaws® T800SS Overburden Bit, reamed diameter 930mm (36.6"), O.D. below drive shoe 795mm (31.3") (1) Conventional C330 780mm (30.7") Socketing Bit |
Hole Size | Pile Size - 900mm (35.4") x 20mm (0.787") wall |
Depth or Length | Piles - Various depths depending on pier location, maximum penetration depth below G.L. 16.8m (55 ft) Sockets - 2.5 to 6.0m (8 to 19 ft) |
Formation | River bed alluvium comprising silty sands, gravels, and cobbles, possibility of cobbles/boulders within soil matrix, 200-600mm up to 1000mm (7-23" up to 40"). Extremely weathered granite 1-3m (3-9.8 ft) grading from highly weathered through moderately to slightly weathered granite, 10-100 MPa (1450-14500 PSI), but overall stronger rock expected, based on failure mode of samples. |
Rig Type | John Holland designed and constructed tripodal leader assembly, mounted on LR-280 Liebherr 280 T crane base. Working weight, including tooling - 320,000 kg (705,480 lbs). Height to top of cat head - 44m (144 ft). |
Description
The project is located on the BHP Billiton Iron Ore Port Hedland to Newman railroad, 112 km (70 mi) south of Port Hedland. As part of BHP Billiton Iron Ore’s planned major increase in iron ore production to 300 MT, Turner River Rail Bridge project is a dual track bridge 225m (738 ft) long, alongside the existing 117m (384 ft) long single track bridge built 38 years ago. The contract includes dismantling the old bridge and restoring the river to its original width.
The new bridge superstructure consists of 15 pairs of 15m (49 ft) long prestressed concrete trough girders, each weighing 95 T, supported on fabricated steel headstocks, and tubular steel piles socketed into granite bedrock. The tubular piles are raked at 1:4 and 1:5, and vertical, the combination depending on the pier location. Total piles are 58, in 2 abutments and 14 piers.
DRILLING METHOD
The bridge foundation design called for the driving of 900mm (35.4″) tubular steel piles to competent partially weathered granite bedrock. The possibility of encountering large boulders above the bedrock at pile locations, which is common in granite areas, made top driving the piles a risky method, as the pile can refuse and the pile toe can be deformed if a large boulder is encountered.
After considering various piling options under such conditions, John Holland selected the proven Numa Super Jaws® under-reaming method to carry the piles down to bedrock.
This method required close consultation between SKM, John Holland and Numa to develop a pile shoe which would meet the pile design specifications and be compatible with the under-reaming bit driving requirements. The resulting pile shoe was 900mm (35.4″) O.D. and 800mm (31.5″) I.D.
DRILLING RIG
The under-reaming method requires lowering the drill tooling into the vertical pile from above, then attaching the pile containing the tooling to the drilling rig. The circumstances of each project determine how this is done. Methods include drilling a cased “rat hole” of larger diameter than the pile, placing the pile in it, and lowering the tooling in (usually a larger bit is not available on the project). Another method is to stand the casing above ground, present the tooling from above using a separate site crane, then move the drilling rig to the tooling and connect up. This requires working from a man basket. David Burnett (mechanical designer) of John Holland proposed building a combination drilling rig based on a large crane, with sufficient travel in the leader to allow the drilling rig to be self contained – i.e. raise the tooling high enough in the leader to clear the pile, pitch the pile using the second crane winch, and lower the tooling into the pile, with all operations performed from ground level. The longest pile on the project is 18m (59 ft), which required a massive, custom designed leader to accommodate the pile and the tooling above it. The specifications of the leader required that it be mounted on a large crane base, and the Liebherr LR-280 was selected. Design, fabrication (in house), erection and site commissioning was under the supervision of David Burnett. This is believed to be the largest self propelled DTH drill rig ever built. The rig is also designed to support a 20 T pile driving hammer, capable of driving piles up to 28m (92 ft) long.
PILING
Piling commenced at the North Abutment on 17 September 2007. After a slow start as operating personnel became familiar with a system they had not used before, piling developed into a steady routine. Piling, pier construction, placing and securing concrete deck girders and demobilisation was completed on schedule, by 21 December 2007.
With experience, the crane (drill) operator became familiar with the downhole drilling conditions by constantly observing the weight and penetration rate on the electronic gauges monitoring the two main winches. By paying close attention to the gauges, optimum drilling rates could be achieved. In the upper alluvial strata penetration rates of 9 m/hr (30 ft/hr) were typical. Drilling rates higher than this would blind the return paths and cause circulation to be lost. In the granite, typical rate in the medium to slightly weathered zone was 3 m/hr (9 ft/hr). This was an indicator that toe level was being reached. At some pile locations, very hard granite boulders were encountered, some of which were only partially in the pile path. Patient establishment of a ledge was required to work through these obstructions.
The 780mm (30.7″) socketing bit with sharp carbide buttons penetrated the granite at up to 3.9 m/hr (12 ft/hr).
The size and arrangement of the drilling rig proved to be a very stable drilling platform, and less wear was observed on components exposed to very high impact and abrasive wear, such as the leading edges on the bit reaming wings, than previously experienced with similar components.
The investment by John Holland in the capital equipment required to undertake major piling projects in the fast expanding Western Australian resources industry is a significant commitment which will be justified for many years to come.